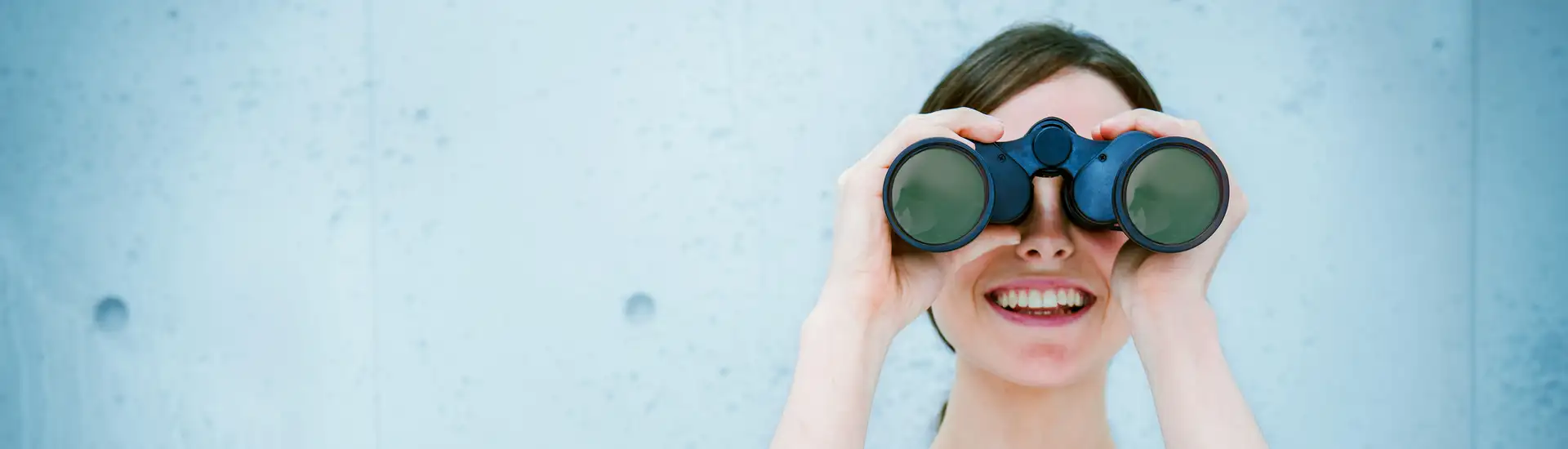
Job portraits from the DURAG GROUP
The DURAG GROUP is a global player with six manufacturing companies, various strategic partners, and numerous sales and service locations around the globe. As representatives of our extensive international team of experts, our colleagues provide interesting personal insights into their working world in our interview series „DURAG GROUP around the world“. It's worth checking back regularly: the series will be expanded over time.
Johanna Gosebrink
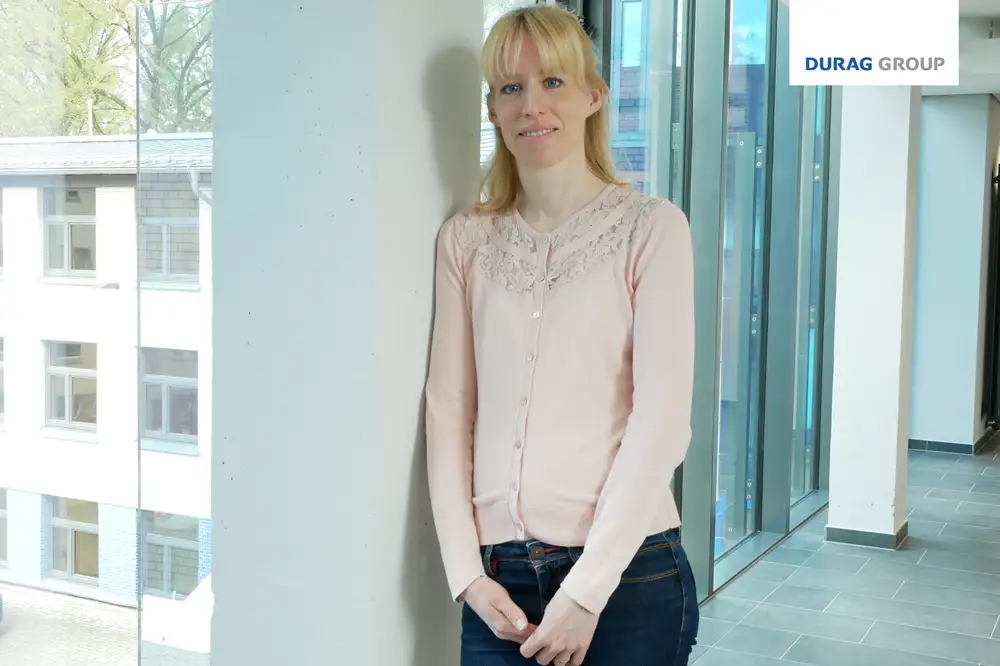
Specialist Academy, DURAG Sales & Service GmbH & Co. KG, Location Hamburg
Career at the DURAG GROUP
- September 2013 – December 2015: Management Assistant / Marketing Manager
- January 2016 – December 2023: Training Manager, Marketing Department
- Since January 2024: Specialist Academy, Business and Organizational Development
Johanna Gosebrink has been with the DURAG GROUP for eleven years in the areas of marketing and training and has been working as a Specialist Academy in the Business and Organizational Development department since the beginning of 2024. Her organizational skills are in demand both professionally and privately: In this interview, the mother of two explains the challenges of her dual role and how she manages to balance work and family life. The working environment at the DURAG GROUP plays an important role. She is also involved as a parent representative in the Parents’ Association of Hamburg and gives us an insight into her voluntary work there.
Johanna, you are a Specialist Academy at the DURAG GROUP. What exactly is your role and what specific tasks do you have in this function within the Business and Organizational Development department?
I am responsible for internal and external service training as well as internal product-related sales training. Specifically, this means that I plan, organize and oversee service training for our customers and partners, as well as sales colleagues in the office and in the field, related to our equipment. I also do the same for internal product training, such as product launches for both inside and outside sales. I particularly enjoy working with all parts of the DURAG GROUP, including the teams from DURAG DATA SYSTEMS, SMITSVONK, HEGWEIN, AP2E and GRIMM AEROSOL TECHNIK.
Organizational skills are therefore extremely important in your professional role, but also because you are the mother of two children, aged three and five. How do you manage to balance work and family?
Organization is everything. However, a lot depends on flexible working hours, the possibility of mobile working and external childcare, in my case the daycare center. If I have to work longer hours or at different times, if a child gets sick, or if external childcare is canceled, I have to find another solution, sometimes at very short notice. I look at the situation from a mother's perspective. However, it is very important to emphasize that work-life balance also applies when family members, such as one’s own parents, need care or assistance.
Do you have any practical tips for other parents on how to balance work and family life?
There should be enough space for both, work and family. It helps to build a network. This can be family members such as grandma, grandpa or friends, godparents, but also neighbors. This is especially true for single parents.
Let’s talk about the employer side. To what extent does the DURAG GROUP support you? Are there any special measures and initiatives that help you in particular?
The DURAG GROUP offers a working time model with the possibility of flextime, so that I can organize my working time flexibly, within certain limits of course. I also get part of my childcare costs reimbursed. The option to work from home is also very helpful.
What else would you like to see?
In my opinion, the DURAG GROUP has understood that well-trained mothers offer considerable potential for the economic success of the company. It has already created some appropriate framework conditions that help me a lot as a working mother. Of course, there is still more to do, for example the proposed four-day week. In this context, too, I have found that my supervisor and the HR department are open to innovation and change.
What challenges do you see for working parents?
Reliable external childcare would be the basis, but unfortunately in my case I can’t rely on childcare at all. I live with my family in Hamburg, and of course this can vary from district to district and from daycare center to daycare center, some parents are more affected than others. However, what is noticeable, is that the situation in daycare centers and schools is becoming more and more precarious.
What is needed in order to promote the compatibility of family and career? How can companies like the DURAG GROUP support parents?
Above all with flexibility. This applies both to working hours and to the place of work, for example working from home.
You are a volunteer on the Hamburg Parents’ Association. Can you tell us more about what motivated you to do this?
For almost three years now, I am involved in the district parents’ committee, some of these members make up the state parents’ committee. To be on the district parents’ committee, you have to be a parent representative in a daycare center, so it’s an ascending system. You can always complain a lot, but if everyone does it and nobody does anything, nothing will change.
What exactly do you do in this volunteer role?
The most active part is my role as a parent representative at my children’s daycare center. I am the first point of contact for the management and the parents. The tasks vary, but I usually get involved when problems arise. First of all, there is the loss and/or reduction of childcare hours. Then there are many other problems, such as children who are aggressive towards other children, children who refuse to eat or drink, teachers who do not behave properly when the fire alarm goes off, group mergers when the day care staff is very ill, to name just a few. There are also other tasks, such as organizing and helping with parties and celebrations, such as summer or farewell parties, garden day, and Christmas caroling. There is always something to do, such as participating in audits, organizing birthday presents, or looking for daycare photographers. The district parents’ committee is increasingly about sharing ideas and, if necessary, passing on problems to the regional parents’ committee.
This sounds like a lot of work. How do you balance work, family, and volunteering for the district parents’ committee?
It works with good organization, flexible hours and locations, and with lots of coffee (laughs). I usually make a to-do list for the next day at the end of the day, but definitely at the end of the week. That way I can keep track of everything and work through it in a structured way. But no matter how well I plan ahead, suddenly the daycare gets canceled, a kid gets sick, I get ill myself, yeah, that happens to moms too (laughs), the car breaks down, or, or, or. As soon as one factor changes, I have to completely reschedule and then things usually get canceled or postponed. I'm very lucky here with my colleagues, who cover for me when I’m away, and with managers who understand my situation and are willing to find individual solutions.
Let’s look into the future. What initiatives or projects are you planning in the DURAG GROUP or in the state parents’ council to support parents?
Due to the federal system in Germany, which also regulates childcare and school education, I am speaking from the perspective of a Hamburg mother. I think it's important to share ideas with each other. Everybody has different ideas or suggestions for solutions, which can also be a solution for their own problems in the respective day care center or school. Basically, I am interested in mutual support and understanding. District and state parents’ council are mainly about raising awareness and putting pressure on politicians and officials. I also supported the petition “Every child counts”. With more than 220,000 signatures, this was the largest petition to the German Bundestag in 2024.
Christelle Gérard
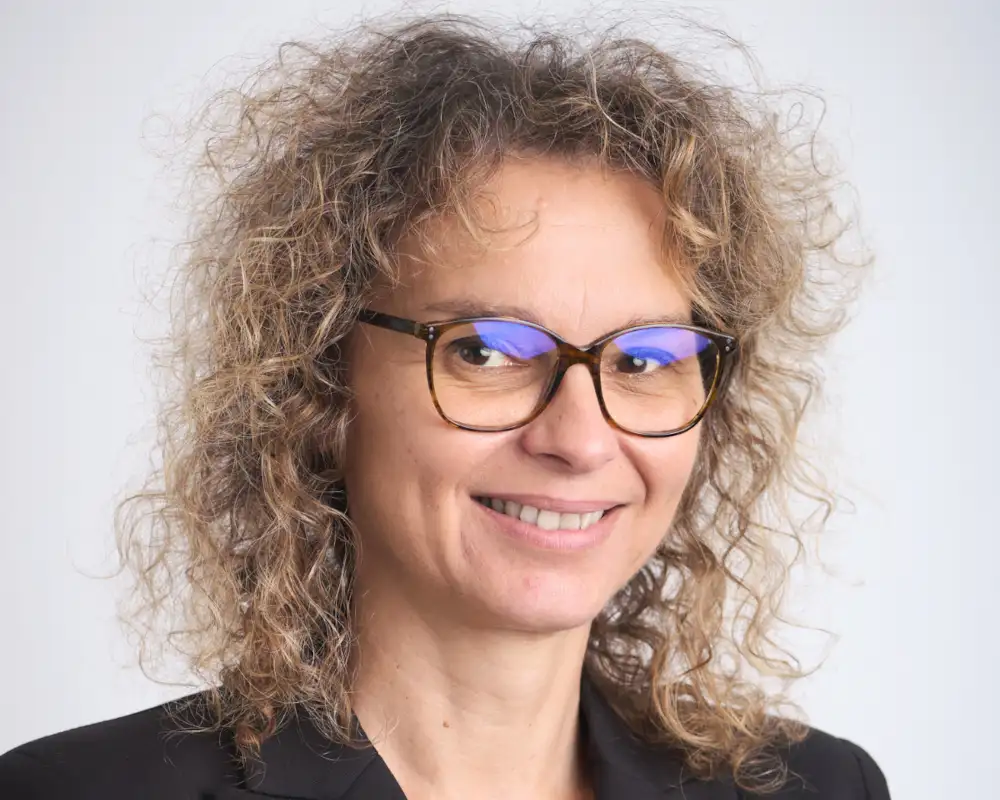
Area Sales Manager, DURAG France, Paris
Positions at DURAG FRANCE
- July 2013 - June 2016: Sales Administration & Execution Manager (maternity replacement)
- Since July 2016: Area Sales Manager
Christelle Gérard is a seasoned sales expert at DURAG France, driving significant sales growth for nearly a decade. Since 2006, the company has expanded its reach, offering products and services from the entire DURAG GROUP portfolio not only in France but also in Belgium, Luxembourg, Spain, and North Africa. In this interview, she shares more about herself and the company.
Christelle, how did you come to the DURAG GROUP and how long have you been with the company?
I joined DURAG France in 2013 to cover a maternity leave as the Sales Administration Manager. Back then, we were a small team of just five people, so I was both the manager and the executive, wearing multiple hats at once (laughs). During those three years, I gained in-depth knowledge of our products and discovered my passion for engaging with customers and driving sales. Fast forward to 2016, when I got promoted to Area Sales Manager. I guess you could say I sold myself on the idea.
What highlights do you particularly remember?
One of the most memorable highlights was the 10th anniversary of DURAG France in 2015, where I was deeply involved in organizing a reception for both partners and customers. Another unforgettable experience was my first client meeting in Belgium. I didn’t have mobile phone, and my brand-new laptop was not yet network-configured. And the technical manager who had all the necessary documents missed the train. So, there I was, scrambling to put together my presentation while riding the train. It was definitely a high-pressure moment, but somehow, I pulled it off and even secured my first order. It was a D-R 820 F, the predecessor of the wet stack dust monitor D-R 909. This is how you learn to adapt and think on your feet, one of the key skills required of a salesperson!
Let’s take a closer look on DURAG France. How long has your branch been in existence and what are its main focuses?
Since 2006, DURAG France, DFR for short, has been offering products and services for the entire DURAG GROUP portfolio in France, Belgium, Luxembourg, Spain and North Africa. The subsidiary, which works with all types of industries, focuses its attention on end users to develop its service activities and offer the full range of products to the market. DFR is very strong in delivering complete, turnkey projects including engineering, products, installation, commissioning and maintenance, using internal resources but also external partners when needed. The main markets in the region are energy from waste, the energy sector, petrochemistry and refinery, cement and chemical industry, steel and glass industry and last but not least university and research laboratories as well as the national Air Quality Monitoring Networks.
Where is DURAG France located and how has the location developed?
The office is situated in the heart of Rueil Malmaison, a western suburb of Paris, just 12.6 kilometers or eight miles from the city’s center. Rueil is renowned for the Château de Malmaison, once the residence of Napoleon and his first wife Joséphine. The town also attracted Impressionist painters like Pierre-Auguste Renoir, Édouard Manet, and Claude Monet, who were inspired by the scenic views of the Seine River that flows through the area. DFR has experienced significant growth over the years, today, we are a key player in the combustion and emission monitoring market. Despite strong competition, DFR has thrived by assembling a highly skilled and complementary team, which played a crucial role in achieving record sales last year, thanks to our ability to diversify and expand our solutions. It's something we’re truly proud of.
Are there any focal points or challenges for DURAG France?
In terms of content and regional focus, one of the primary challenges for DFR is navigating the competitive landscape, demanding continuous innovation and differentiation in product offerings. Additionally, staying aligned with evolving environmental regulations and customer expectations in France and the broader European market requires constant vigilance and adaptation. The DURAG GROUP as a whole also benefits from these efforts and the corresponding successes.
How do you assess the development potential of DURAG France?
The development potential of DFR’s location in the western suburbs of Paris is substantial. Its proximity to one of Europe's major economic hubs provides access to a vast talent pool and potential clients, fueling further growth. Moreover, as environmental regulations in France and Europe become increasingly stringent, the demand for advanced monitoring solutions like ours continues to rise. DFR is well-positioned to seize these opportunities, leveraging our skilled team and innovative product portfolio to strengthen our market presence and drive sustainable growth.
What do you wish for personally and for DURAG France?
I feel part of a big DURAG family, which is expanding in France, now counting almost 100 people across DURAG France and AP2E. I'm proud to be part of this team and wish it all a bright future. Personally, I wish to see the DFR continue to grow, strengthen its leadership position and remain a source of inspiration within the DURAG GROUP. I want our team to keep flourishing, leveraging its diverse talents and unique spirit of collaboration, to drive innovation and success. To further strengthen our local presence, we have recently created a dedicated LinkedIn page for DURAG France in addition to the general DURAG GROUP LinkedIn profile, allowing us to communicate with our partners in French. I look forward to welcoming many new followers to our social media channels and seeing this community grow to continue our journey together with the same passion and commitment.
Narendar Londhe
Technical Consultant / Customer Service, DURAG India, Bengaluru
Positions so far at DURAG India
- October 2018 – March 2021: Senior Sales Engineer
- Since April 2021: Technical Consultant / Customer Service
At the beginning of 2024, our customer service team in Hamburg had a special guest for a few weeks: 45-year-old Narendar Londhe, Technical Consultant at DURAG India. He was trained in CRM and SAP at the Kollauhof site by actively working with his colleagues on day-to-day projects. Since mid-March, he has been applying what he has learned in his job at the Bengaluru site. In this interview he tells us more about his time at the river Elbe, the history of DURAG India and his tasks within the company.
Narendar, what exactly is your role at DURAG India and how and when did you join us?
I am a bachelor's graduate in Instrumentation Engineering and have a diploma in the same field. I applied for a vacancy as a sales engineer in 2018, went for two interviews and got the job as a senior sales engineer at DURAG India in Bengaluru in October 2018. Initially, my responsibilities included preparing quotations for various products, tender submissions and calculations. I was also responsible for responding to technical customer queries, customer meetings and maintaining ISO related documents. In 2021, I was transferred to Customer Service as a Technical Consultant. My job profile was expanded to include creating additional CRM opportunities, registering suppliers, preparing order confirmations and holding order meetings with the production, engineering and shipping teams.
Can you tell us more about the branch?
DURAG India was established in 2002. The history of this DURAG GROUP location began in 1997 with a liaison office in Secunderabad. A branch office in Bengaluru followed in 2002 and in 2006 DURAG India Instrumentation Private Limited was established. Our new modern office building in Bengaluru was celebrated with a grand opening in May 2022. Although the actual move took place on October 1, 2021, the official inauguration could only take place a few months later due to the pandemic. The company's headquarters are located in Peenya, the industrial hub of Bengaluru. The total number of employees is currently around 35 in production, assembly and back office. It is a spacious three-story building, with the first floor dedicated to product testing, packaging, warehousing and material loading. The second floor houses the calibration department, a training and conference room, the assembly and cabling area, and the workstations of the production and service managers. The third floor houses the offices and the canteen.
What are typical characteristics of the local work culture in India and to what extent does the DURAG GROUP benefit from this?
Our team is characterized by a high degree of flexibility, commitment and an open work culture; we value communication and transparency. As a result, employee turnover is low and everyone is constantly working to maximize their personal skills and, in turn, increase productivity. I think that speaks for itself.
What are your personal highlights so far at DURAG India?
On an annual basis, training and interactive sessions are organized with the employees of the distribution partners on the subject of DURAG GROUP's products and services. This event is designed to share ideas and discuss customer requirements for specific applications in different geographic areas. Of course, we also discuss competitive products and much more. It lasts two to three days and always impresses me due to the live interaction with the employees. We learn about their challenges, and they understand our issues with respect to the daily working priorities.
You came to Hamburg to support DURAG GROUP's customer service team of the site and learn at the same time. How did this come about?
My stay was initiated by the customer service and sales managers in Hamburg. The first ideas were put forward in November last year and I started working there in January 2024. It wasn't training in the traditional sense, as I worked on typical tasks as part of the team until mid-March. All the tasks I learned in Hamburg are part of my job description in my home country, so I can apply almost 90 percent of what I learned in my work in India. Immediately after my time in Germany ended on March 15, I took over the corresponding tasks in the office of DURAG India.
What was the content about?
I learned a lot of new things in the CRM area, for example about different types of tickets. All incoming requests are registered through this ticket system. It was about the process steps involved in solving and processing them. We also talked about generating an order and sales ID and creating order confirmations with the SAP tools. My new role in India includes tickets for the Asia Pacific region and has recently been expanded to include Europe, Middle East and Africa.
Were there any special experiences in Hamburg during your stay?
I enjoyed the very good personal exchange with the technical team, where we discussed our approach to certain work projects and the challenges involved. On a social level, the "Hamburg Cleans Up" event on March 5 was new and impressive to me, as we cleaned up the area around the Kollauhof site. And in the last week of my training, a farewell breakfast was organized for me, which was really good and I really enjoyed it. I also enjoyed the private dinners with friends, but also with superiors and colleagues such as Konstanze Müller, Head of Customer Services, and Ujjwal Thakur, Technical Consultant. By the way, the DURAG GROUP rented an apartment especially for my stay and gave me a “Deutschland-Ticket” for the time, a ticket that allowed me to use all public transportation in the country. This way I was able to travel a lot in my free time and went on various day trips to experience German culture up close. I went to Berlin, Lübeck, Lüneburg and Bremen.
Markus Pesch
Senior Expert Ambient Air, GRIMM AEROSOL TECHNIK / DURAG GROUP, location Friedersorf
Positions at GRIMM AEROSOL TECHNIK - a DURAG GROUP company since 2015
- 2008 - 2014: Technical Director incl. scientific sales at GRIMM AEROSOL TECHNIK
- 2014 - 2020: Technical Director and Head of Development at GRIMM AEROSOL TECHNIK
- 2020 - 2023: Manager for Training & Development
- Since 2023: Senior Expert Ambient Air
Markus Pesch, born in 1965, holds a doctorate in technical environmental protection and has been Senior Expert Ambient Air since 2023. His career with us began at GRIMM AEROSOL TECHNIK. The company, based in Friedersdorf, specializes in innovative solutions for the detection and analysis of aerosol particles in various areas such as environmental monitoring, workplace safety and research. In this interview, family man and passionate triathlete Pesch talks about the company's structures and processes, as well as the unique team spirit.
Markus, how and when did you join the DURAG GROUP?
I first came into contact with the DURAG GROUP in 2015, when Hans Jürgen Grimm decided to sell the company named after him. At the time, it was important to him to hand it over to a German company that was active in a similar field to GRIMM AEROSOL TECHNIK. He wanted to bridge the gap between emissions and immissions. At that time, I helped him to introduce the company to the DURAG GROUP. It was then taken over in the fall of 2015.
What was your career like before that, what training did you do and when did you join the GRIMM AEROSOL team?
Before my time at GRIMM, I studied technical environmental protection engineering at the TU Berlin, specializing in air pollution control, and completed my doctorate on ozone as an air pollutant under Professor Gerhard Israel. He was a luminary in the field of air pollution control and aerosols and many years ahead of his time. My first contact with GRIMM was during my time at university as part of a research project in Berlin to analyze the causes of PM2.5, particulate matter with a diameter of less than 2.5 micrometers, and ultrafine particles with a diameter of less than 0.1 micrometers. Nano-measurement technology and the EDM 180 particulate matter measuring device from GRIMM were used. After a visit from GRIMM's managing director, I decided to switch to the business world, despite my ties to the university. The opportunity to develop personally in a company with a global brand presence convinced me.
Can you tell us a bit more about the history of GRIMM AEROSOL TECHNIK?
The company was founded by Hans Jürgen Grimm over 40 years ago in Ainring, where he lived. Due to the company's growth and the production and development manager at the time, another branch was founded in Pouch. In 2018, the DURAG GROUP acquired a new building in Friedersdorf, which has since served as the location for production and development. It offers sufficient space for additional staff and expanded production capacities. The investments in this region are significant and demonstrate the group's commitment. Around 50 people are currently employed in Friedersdorf, while seven employees work in Ainring.
How has the site developed?
It has developed significantly in terms of structures and processes in recent years. This has also been well received by customers. The expansion of the premises also means an increase in production capacity. The sense of togetherness that we promote through joint activities should be emphasized. We have a strong team spirit and this contributes significantly to the success of our site. However, we also face the challenge of recruiting skilled workers.
What highlights do you particularly remember?
During my time at university, I was used to giving presentations - but not in French. Accordingly, my presentation at the "Ambient Air Day" in Paris with DURAG France was something very special for me. Another highlight for me was the "I2SM" in Mallorca, where I was able to present GRIMM AEROSOL TECHNIK of the DURAG GROUP. My presentation was awarded with a trophy in the shape of a flame as the best presentation of the event. This has had a place of honor in my office ever since. I also have fond memories of the DURAG GROUP partner meeting in 2023 and the first ambient air training for colleagues from the DACH region at the end of 2022. We had an incredibly good atmosphere in Friedersdorf and the feedback from the participants made me really happy!
What are you currently working on?
I'm working with the Academy department to develop a training series that uses videos and web-based training (WBTs) to teach ambient air content. This includes basic knowledge about aerosols and gaseous air pollutants as well as information about the measuring devices. The focus is on the diverse and fascinating applications of our devices. The training courses are divided into different knowledge levels and require no prior knowledge. I have a good feeling that I can make a difference in this area and help our group of companies move forward. The fact that AP2E's ambient air division has now been added to the mix is simply brilliant. Their OFCEAS measuring principle in combination with LPS is the best and most fascinating thing I have ever come across for gas measurements. As with GRIMM, the aim now is to get all that horsepower onto the road even better.
Finally, how do you rate the development potential and what would you like to see?
Our development potential at the GRIMM AEROSOL TECHNIK site in Friedersdorf is very promising. Thanks to the brilliant measurement performance of our devices, we have an excellent basis for optimizing them even further. I am convinced that by focusing on our core competencies and hiring additional staff, we will be able to achieve many of our goals in the future. Strong sales and internal training programs also play an important role here. For the future, I hope that we will be able to retain qualified employees in the long term by continuing to invest in their development and offering them prospects. We have already achieved a great deal within the DURAG GROUP in recent years. If we can convey this spirit even more strongly to the outside world, I see many more opportunities and growth potential.
Jacqueline Tavares Guimarães
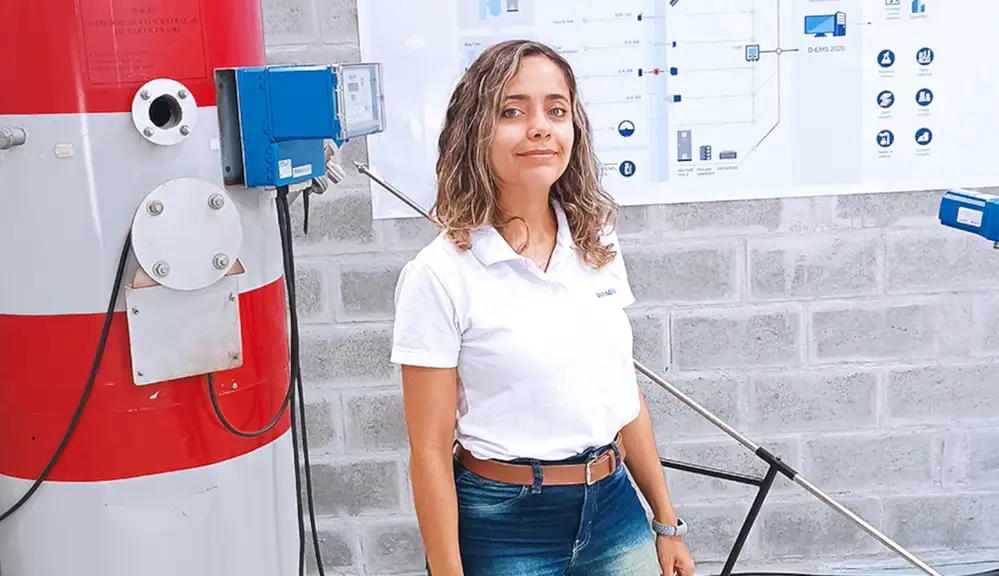
Service/After Sales, DURAG BRASIL
São Paulo, March 2024 - 32 year-old Jacqueline Tavares Guimarães from São Bernardo do Campo, São Paulo, works in after sales and service at DURAG BRASIL. The independent company is the regional sales office of the DURAG GROUP in Brazil. In this first interview of our new series “DURAG GROUP Around The World”, she talks about her beginnings at the company, which was then known as DURAG Siena and looks into the future with us.
Jacqueline, what is your job with us, how did you come to the DURAG GROUP and how long have you been with us?
I started as a Sales Assistant in the commercial department at DURAG BRASIL in mid-July 2014, when it was still called DURAG Siena. I currently work in After Sales and Service, where I coordinate the local service activities.
What highlights do you particularly remember from this time?
I particularly remember two training days that we held for our sales partners some years ago. Not only did we gain additional valuable insights into our overall product portfolio, but we also got to know our partners better - an excellent basis for further cooperation. In addition, I also have fond memories of the 2014 World Cup when I watched the Germany vs. Brazil game with my colleagues. It was fun to cheer and get mad when our team lost, we spent a lot of time together during this World Cup in our home country. And a third highlight: we now organize “Churrasco” or BBQ in a restaurant to celebrate reaching a sales target. Furthermore, the “DURAG Academy” learning platform is a great way to expand our knowledge, and the access to the head office with tools such as Teams or CRM makes our collaboration very effective.
Can you give us some information on the location and size of DURAG BRASIL? How has it developed and what were the challenges?
The branch is located in São Paulo, Diadema City. From here, the company operates throughout Brazil as DURAG BRASIL, supported by sales partners and as part of the international DURAG GROUP. Since the DURAG GROUP entered the Brazilian market, the company has developed steadily. To date, we have had to deal with several economic crises in Brazil, but especially in the last two years, we have been able to significantly increase the sales of DURAG GROUP products. Since 2022 the company operates under the new name DURAG BRASIL.
Are there any content or regional focuses and challenges?
Personally, it was a big challenge to start in an area where I had little prior knowledge. But I like to learn myself and I also enjoy sharing my knowledge and experience directly with my colleagues After all, an introduction to the company's processes is also important for new team members so that they know how to approach their tasks. In my new role in After Sales and Service, there are also many new challenges and things to learn. However, I particularly enjoy supporting my team and growing together with them.
How would you describe your corporate culture and what would you personally wish for the location?
In a constantly evolving working environment, respectful interaction and teamwork are fundamental aspects of our day-to-day business. Due to the size of our team of ten, we are able to gain experience in a wide variety of areas, but we also have to share our knowledge efficiently so that all processes run smoothly. I hope that this respectful and result-orientated cooperation - hand in hand - will continue in the future at DURAG BRASIL.
Matthias Schultz
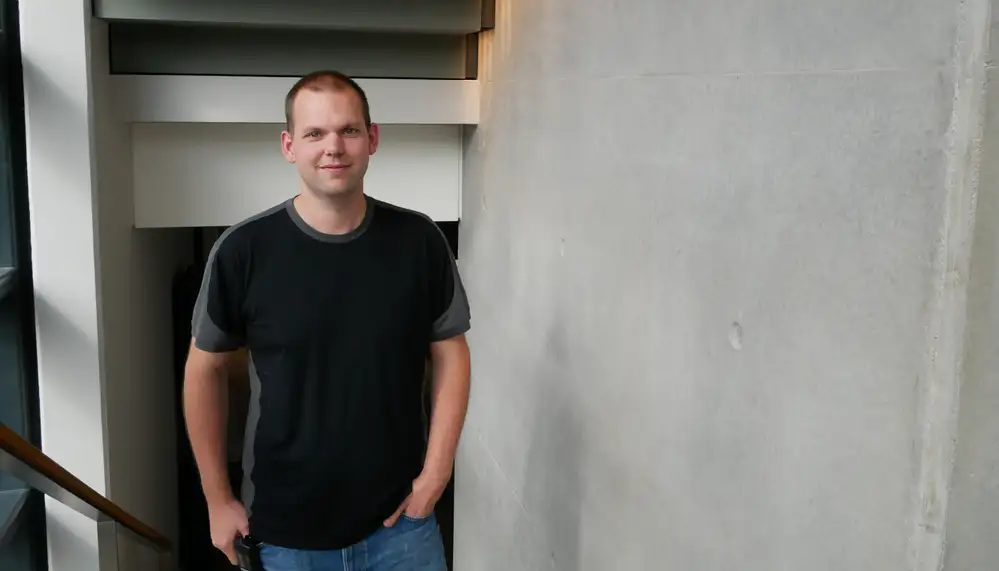
Deputy Head of mechanics department DURAG GROUP, Hamburg
Hamburg, March 2024 - Matthias Schultz is the Deputy Head of mechanics department at DURAG GROUP. The 37-year-old started with us as a cutting machine operator in 2010 and has since experienced the change in production at first hand. Read more about the automation and digitalization process at DURAG GROUP here.
Automation and digitalization of metal cutting: From bar loader to high-tech machine
In 2010, Matthias Schultz's first year at the DURAG GROUP, there was already an automation solution: a bar loader was used to load the relevant material into a CNC lathe. Since then, however, a lot has happened in his field of work. For the past three years, a robotic pick-and-place machine has also been used in production: sawing sections are automatically loaded and unloaded in its turning center. Matthias Schultz looks with us at the DURAG GROUP's path to more digitalization and efficiency.
Schultz started in 2010 as a cutting machine operator in the DURAG GROUP's production department at the Hamburg site as part of a temporary employment agency; after a year, he was hired permanently. In 2023, he took over the position of trainer and, since the same year, he has been deputy head of the mechanics department, where he works with a team of 21 colleagues.
Technical progress has changed his everyday work: "I used to literally stand at the machine all day to load and unload workpieces." In his early days at the DURAG GROUP, components were usually produced on several machines. After drilling, it was off to the milling machine to insert holes or threads, for example.
Highly modern machines for greater efficiency
In the recent past, the company has invested in high-tech equipment that can do both: turning and milling. "Today, a single machine is set up and the robot's workpiece storage is loaded, followed by the complete machining of the components," says Matthias Schultz. Immediately after setup, the person responsible has enough time to devote to other important activities in the production process. "In this way, we save at least one work step and have been able to reduce the time per production order," says the Hamburg native. "From 2020, the year before automation, to 2022, we were able to increase the system's productive time by 57%."
Currently, two of the nine CNC lathes and milling machines in the cutting department enable six-sided complete machining. They work independently and without manpower for a second shift. "A raw part is inserted and a finished workpiece comes out at the end," explains Schultz. The automatic loading of the workpieces also guarantees significantly higher repetition accuracy and precision during the clamping process.
The existing NC program of the processing machine works very simply. It is controlled by numerical instructions and carries out very precise movements and work steps. "Eight parameters have to be entered on the robot in advance. The jaws are then changed and the robot is ready for use. It feels more difficult to use a smartphone," says Matthias Schultz with a twinkle in his eye. Before the robot was introduced, only a two-day training course was required.
Automation, digitalization – and soon AI as well
Particularly with regard to certain parts, automation at the DURAG GROUP is a success story in his eyes. "The components used to be delivered fully machined by the foundry," recalls Schultz. "However, due to bottlenecks during the COVID-19 pandemic, our supplier was only able to deliver the raw parts. So we machined the parts directly on our premises." Thanks to the automated system, production was able to run for almost 24 hours.
"Automation and digitalization are becoming increasingly important in order to remain competitive," says Schultz. "AI is also not that far away in the manufacturing sector." Highly qualified employees who stand at the machine all day, however, will no longer exist. Due to the shortage of skilled workers, there is no way around more automation and digitalization. On the one hand, employees need to be relieved of simple tasks so that they can focus exclusively on complex activities that match their qualifications. On the other hand, higher utilization of the processing machines means greater efficiency.
The 37-year-old is confident about the future of his area of work: "Here at the DURAG GROUP, we have successfully taken the first steps in the right direction. I firmly believe that we will continue on this course. I am convinced that the acquisition of new CNC processing machines will not be possible without automation solutions. And with regard to the digitalization of production, I still see potential for us.".
Verena Buchem
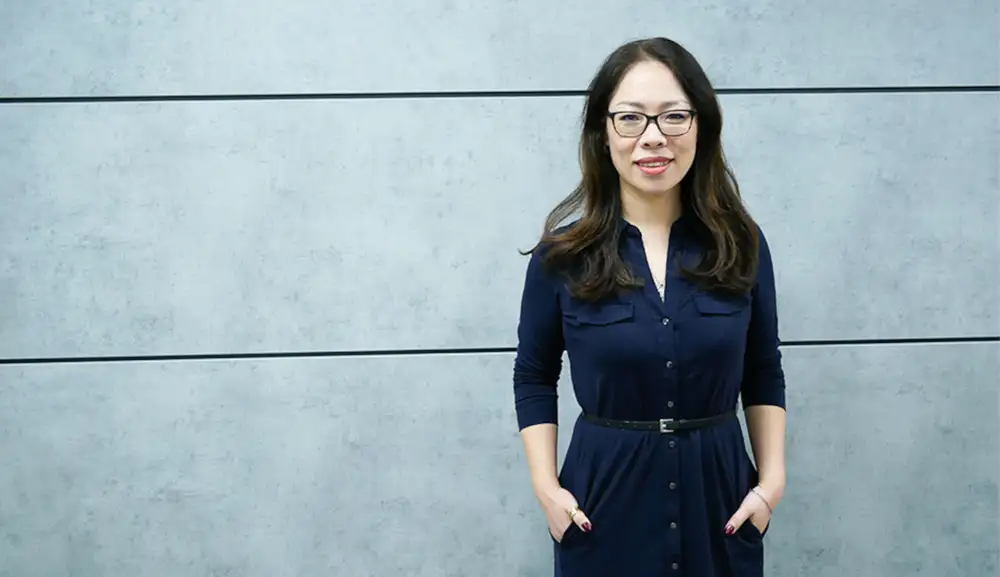
PEM Product Portfolio Manager DURAG GROUP, Hamburg location
On the occasion of the International Women's Day on March 8, we talked to Verena Buchem. She has been with the company since 2018 and is experiencing how more and more women are taking on team leadership and department management positions. She herself is currently Product Portfolio Manager for the PEM business area. The 37-year-old mother of a son talks about her own career at the DURAG GROUP and talks to us about a business world in transition, towards more equal rights for women.
Verena, International Women's Day has been celebrated on March 8 for around 100 years and is not least about equality in the workplace. How do you personally experience the changing role of women in the business world?
After completing my degree in biotechnology & process engineering, I worked in a mechanical engineering company. Unfortunately, it was still taken for granted that I, as a woman, wrote the notes in meetings. And verbal discrimination had to be accepted "because that's just the way it is". Today, I'm noticing a big change: more and more people recognize sexism when they see or hear it. And they dare to address it openly in the respective situation, which is a great development. Nevertheless, it is women rather than men who notice such things. I am convinced that we need more male advocates who develop a sensitivity for feminist issues. We must not forget that corporate cultures around the world are male-dominated. Women have only been allowed to vote in Germany for around 100 years. We women have only had equal rights before the law for just under 65 years. And we have only been allowed to decide for ourselves whether and what we work for 47 years. Against this background, the status quo is not surprising. It is now up to us and our male colleagues to create a new culture.
How far does the DURAG GROUP ensure equal opportunities for female employees and how has the number of female employees developed over the years?
I have only been with the company since 2018, but I have noticed a change; there are more women in team management and department management positions than six years ago. Nevertheless, women are still more likely to be found in commercial, HR or marketing roles. However, this is not due to the DURAG GROUP, but to our fundamental social norms and conventions. Regardless of gender, the DURAG GROUP offers development opportunities to all employees. However, I think there is still potential for more educational work, programs and initiatives on the subject of diversity, an equal corporate culture and equality.
What exactly is your role at the DURAG GROUP?
I started in April 2018 as Product Manager for our total mercury analyzer. I was subsequently responsible for other products in the PEM portfolio. Then I became mother of a son and since returning from parental leave in April 2022, I have been working as a Product Portfolio Manager for the entire PEM area. Since February 2023, I have been supporting PEM Product Management and Technical Documentation in a restructuring process.
What highlights do you particularly remember?
My role gives me the privilege of working all over the world. International conferences, customer visits and meeting our long-standing sales teams and global partner network inspire me. The diversity of people, characters and cultures gives me new inspiration every time; every encounter, every experience contributes to my personal development. I am very grateful for the opportunity to experience this.
Do you have any impact on the younger generations of women at the DURAG GROUP and what do you wish for future female employees in the company?
We have great young women here. And one of the roles I have chosen for myself is to be a role model for future generations (laughs), but women or men are honestly of secondary importance. I hope that my way of dealing with people and my way of working will be motivating in a positive sense. If I've inspired just one woman to "stand her ground" in the last few years, then I've already achieved a lot. But one thing is certain, women need to support, encourage and challenge each other. We will perhaps always be in the minority in our industry. We therefore need to actively celebrate our skills, our values and, last but not least, our femininity in order to make the best decisions and thus improve cooperation in the long term. I would like future generations of women in the company to be aware that women who choose our industry have a special fighting spirit from the outset. We don't have to adapt to the masculine corporate culture; we are exactly as good as we are. This allows us to contribute huge added value to the company's success.
Stefan Kägi
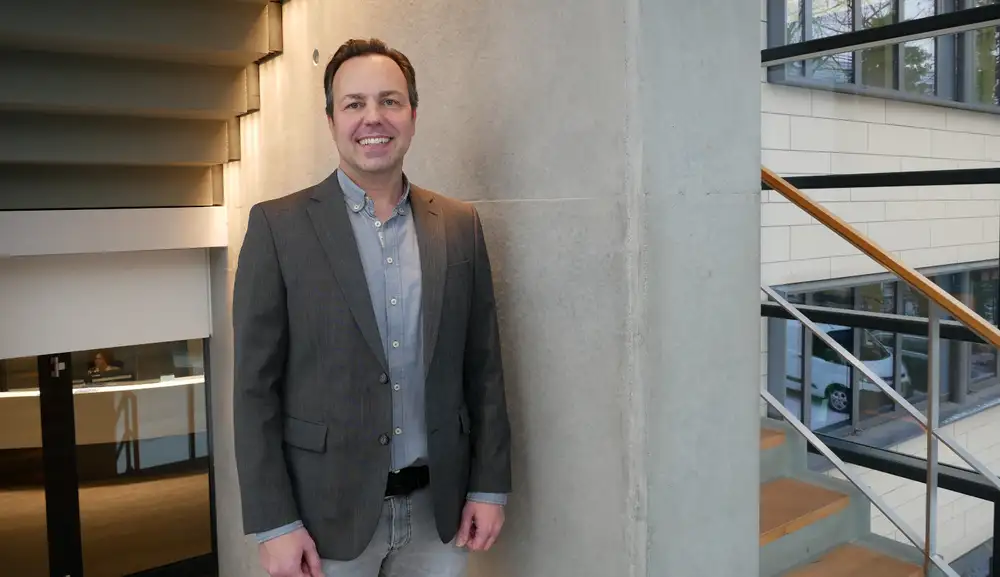
Human Resources Administrator, DURAG Holding AG, Hamburg location
DURAG milestones:
- 2005: Start of apprenticeship as industrial clerk
- 2008: Completion of apprenticeship, work in financial accounting department
- 2009: Trainer for industrial clerks at the Hamburg location
- 2020: Move from financial accounting to human resources management
- Since 2021: Trainer for student trainees
Stefan’s career at DURAG GROUP started in 2005 with an apprenticeship as industrial clerk, which he completed successfully in 2008. After several years in financial accounting, he moved to the human resources department in 2020. He took most of his previous responsibilities with him, but was able to devote more attention to the next generation of professionals than before. You can read here why the topic of training is particularly close to his heart and what makes DURAG GROUP so appealing to him.
How did it come about that you applied to DURAG GROUP?
"I had already completed a first apprenticeship as an energy electronics technician at Beiersdorf, but found that it wasn’t the right fit for me there. While looking for a second apprenticeship, I came across a job ad for DURAG GROUP. The medium-sized company size and the short distances between departments immediately appealed to me, based on my impressions at Beiersdorf."
What are your main activities and which of them do you particularly enjoy?
"I look after our trainees, the interns, and the topics of time management and vehicle fleet. I’m also a trainer for our industrial clerks, including those who are also studying. I particularly enjoy the role of trainer. I get to work with mostly young people and give them the opportunity to learn their occupation of choice, to make the most of themselves later in their career and to continuously develop themselves on the basis of their training."
You have been training the next generation of DURAG GROUP employees since 2009. What exactly appeals to you about your job as a trainer?
“Working with young trainees, providing assistance, discussing worries and needs in some cases and coming to a good result in the process – that’s the beauty of my job. I’m also involved in organizing inter-year and inter-training gatherings such as the induction week, team-building activities, project weeks and Girls & Boys Day. These are exciting and important events for our apprentice industrial clerks, electronics technicians and machining mechanics, but it’s also an important and intensive time for us trainers.”
Were there any experiences or projects during your time at DURAG GROUP that particularly impressed you?
“Two examples come to mind. I think the early recognition of potential in trainees is tremendous. In my time as a trainer, there were many such cases. With one of our trainees, we already knew in her first year of training what position she could fill after her training. After consulting with her, the open position was taken care of internally for a year and a half and kept open for her. The apprentice naturally moved into this challenging position after her apprenticeship and also progressed from there step by step.
Another example is how the employees deal with new developments. DURAG GROUP has evolved continuously. On the way to becoming a modern company, it was often necessary to introduce new software and ERP systems. These new systems were supported by the open and broad-minded nature of my colleagues and implemented quickly with a lot of work, diligence and commitment. This attitude – of being open to new things – has always surprised me in a positive way.”
What distinguishes DURAG GROUP from other employers you have known?
“I find the pleasant size of the company positive, and also the nice sense of togetherness and the shared events. The chances of promotion – with the right qualifications – are significantly higher than at other companies. And of course the training is of a very high standard. We see ourselves as being on an equal footing with our trainees even during their training.”
Andreas Bauer
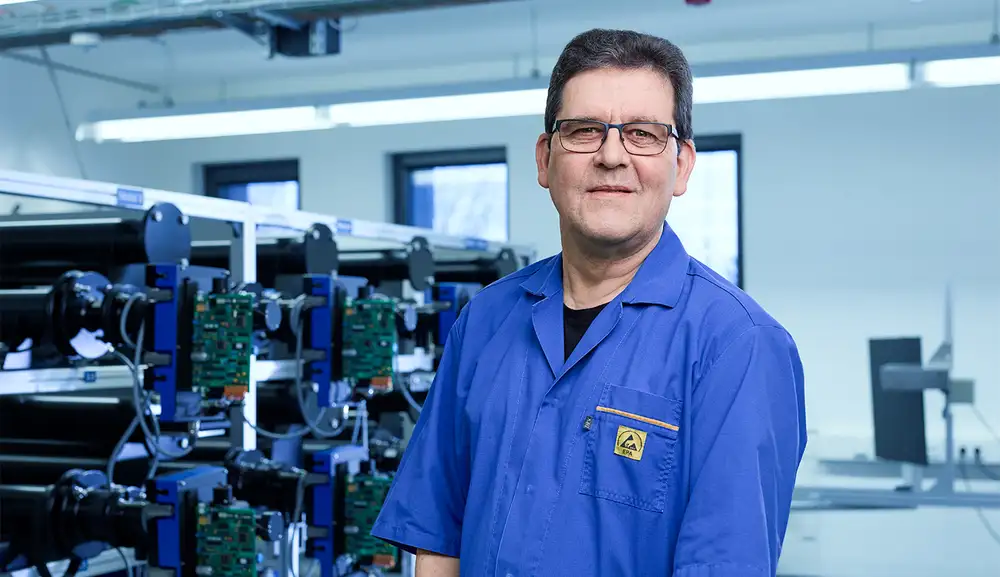
Head of the Electronic Series Production and Repairs department, DURAG GmbH, Hamburg location
DURAG milestones:
- 1979: Start of training as an electronics technician for precision engineering
- 1983: Taken on as technician after apprenticeship
- 1987: Head of Flame department (electronic single part production, combustion technology)
- 2015: Head of Electronic Series Production department
- 2019: 40th company anniversary
- 2020: Head of Repairs department
Andreas started his apprenticeship as an electronics technician for precision engineering at the DURAG GROUP in 1979 and has now been with the company for over 40 years. After completing his apprenticeship, he was taken on as a technician and subsequently rose to the position of department manager for electronic series production and repairs. Read here about the milestones in his career and the challenges and highlights of his daily working life.
What were the most important milestones in your career?
“Back then, today’s apprenticeship as an electronics technician for devices and systems was offered in two steps, with your apprenticeship as a mechanic followed by training as an electronics technician.” And this is indeed the way Andreas chose to do it at the DURAG GROUP. After completing his training, he was taken on as a technician and just four years later, Andreas was made head of the Combustion Technology department. “As a young man of 25, that was a lot of responsibility to assume – but it was also formative for the future.”
2019, Andreas celebrated his 40th anniversary with the company: “If I hadn’t felt so comfortable here, well I wouldn’t have stayed on.”
What does your work consist of?
Andreas currently heads up both the Electronic Series Production department, which produces flame monitors and instrumentation for environmental metrology, and the Repairs department, where he is responsible for a team of 40: “When I see potential, I try to nurture it.”
His work includes ensuring that deadlines are met, administrative tasks and the monitoring of material stocks: “My job is to keep production running.” Andreas is also responsible for the continuous improvement and ongoing development of procedures and processes.
What developments have you seen during your time with the DURAG GROUP?
At the beginning, the DURAG GROUP was a medium-sized company with a focus on the German market. Thanks to technological progress, it is now possible to manufacture larger quantities and serve an international market. Compared to today’s possibilities, Andreas says the production of that time was like a “craft shop”.
“Even though change can create resistance, it’s good for a company as long as it becomes part of the culture.”
What are the challenges and highlights for you?
“Alongside training and taking on the running of the department, one of today’s highlights is that we can achieve unit quantities we didn’t even think were possible in the past.”
What makes the DURAG GROUP special for you?
“Every possible effort is made to respond to the needs of employees. I like the fact that the atmosphere has remained so friendly and informal despite the growth we have seen. The technology that goes into DURAG GROUP products is very interesting and innovative.
And last but not least, we build products for environmental protection – products you can stand behind!”